TRANSFER PROCESS OPTIONS AND ACCESSORIES FOR THE FOOD INDUSTRY
A COMPLETE RANGE OF PRODUCTS FOR YOUR FOOD TRANSFER EQUIPMENT
Cross-contamination issues are a source of concern for LPNs.
It is essential to prevent the spread of germs and cross contamination of food products in order to obtain a safe and efficient professional environment over time.
Ideal solution in terms of hygiene, the GMMI pipe transfer equipment is easily cleanable and is based on equipment 4 x less energy, 7 times more powerful and 2 x less noisy.
GMMI, specialist in food transfer lines, helps you meet this challenge with solutions adapted to your needs with a full range of washable transfer systems (NEP / CIP).
Our pipe transfer range includes several options:
- CIP / CIP (cleaning system)
- Screen
- Directional switch
- Receiving cyclone
- Volumetric laser detector
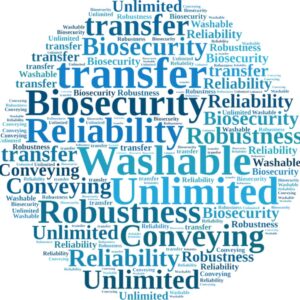
CLEANING-IN-PLACE OPTION FOR FOOD TRANSFER MACHINES
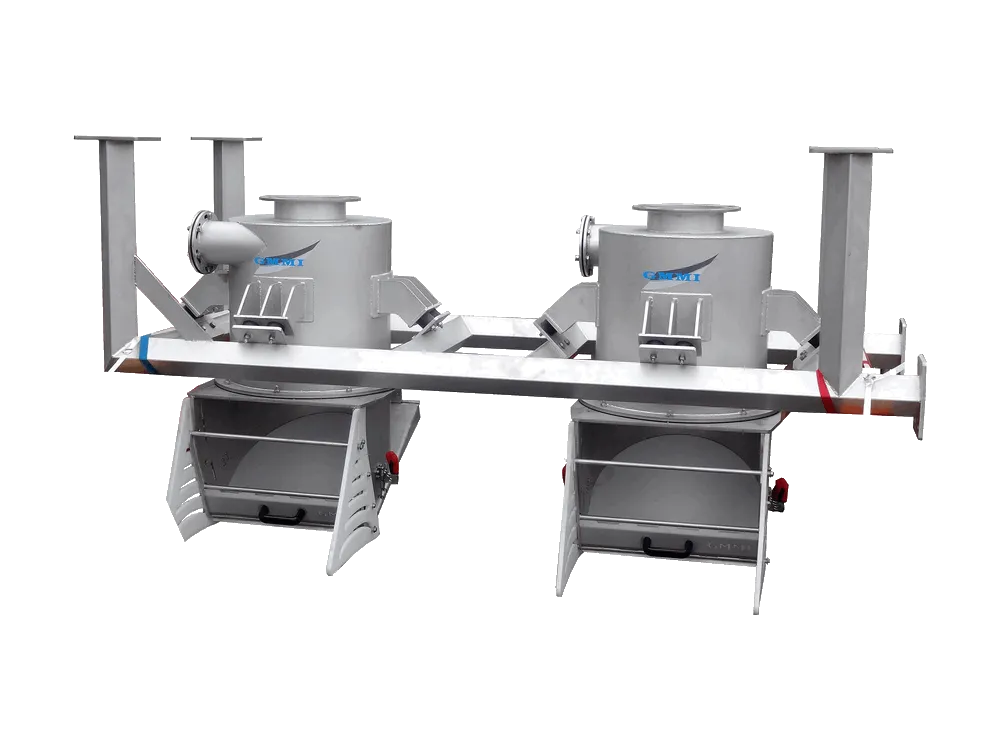
RECEPTION CYCLONE
Adapted to the product and the environment, the cyclone reduces the speed of the product transferred at high pressure. It is also used to load products by gravity into palbox bins, or on conveyors in production rooms.
BIN TIPPER
A secure hydraulic solution for loading the Gicompress
The bin tipper is a piece of equipment designed to facilitate and automate the loading of the Gicompress, eliminating manual handling. It is particularly suited for facilities using standard bins, which are traditionally moved by workers.
Powered by a robust hydraulic system, the tipper lifts fully loaded bins weighing up to 1 ton and empties them in a single smooth motion into the Gicompress, thanks to a tilting angle of up to 130 degrees.
An enhanced safety system
Several features have been incorporated into the equipment to ensure operator safety:
Light curtain (laser sensor): If a person enters the safety zone, the system detects their presence and immediately stops the tipper’s movement.
Manual lift control with safety hold-to-run function: To perform the tipping motion, the operator must maintain constant pressure on the button for the entire duration of the rotation (approximately 15 seconds). If released, the lifting stops immediately.
This equipment saves time, secures the loading process, and eliminates risks related to manual handling.
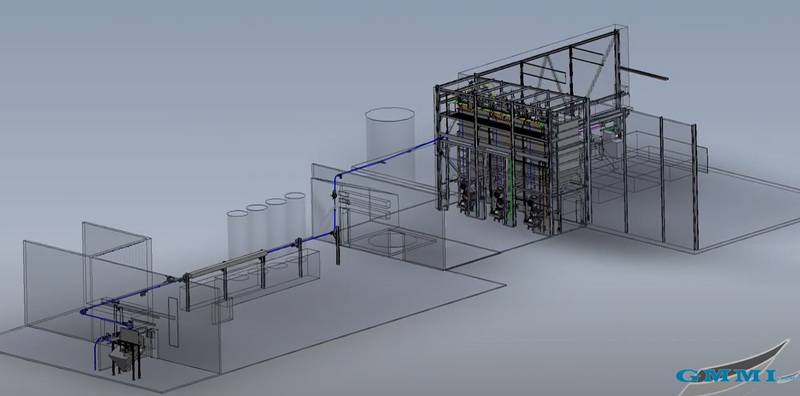
STORAGE TANK
The storage tank has a capacity of up to 60 m3, adapted to customer requirements, and is designed to accommodate all types of product and by-products. Loaded and unloaded using our transfer technology, it enables products to be stored at ambient temperature, avoiding any risk of cross-contamination. They can also be fitted with weighing cells for precise measurement of stored quantities.
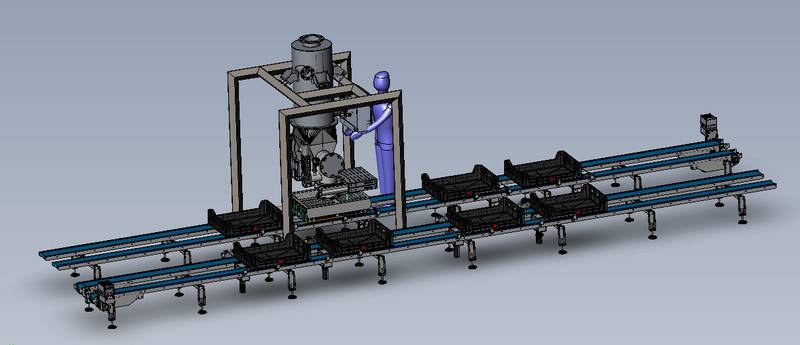
FILLER
The filler is used for weighing a continuous flow of products, using either volumetric or weighing cell dosing, depending on the customer’s specific requirements. It can be configured for either volumetric or subweighing, for high dosing accuracy. And to guarantee precision, we use a drip valve to optimize product drop.
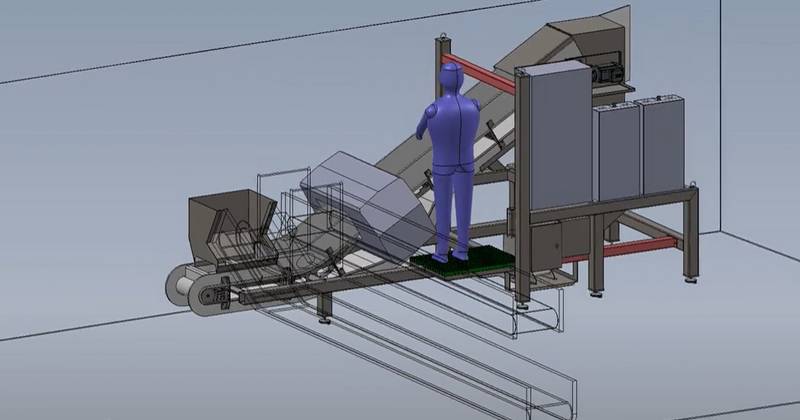
LOADING CONVEYOR
The loading belt enables your products to be loaded in synchronisation with the operation of the GIBAIR conveyor. It makes loading easier, smoother and fully automated, giving you complete control over the performance of your transfer pumps, and optimize the reduction of labor cost and manual handling needs.
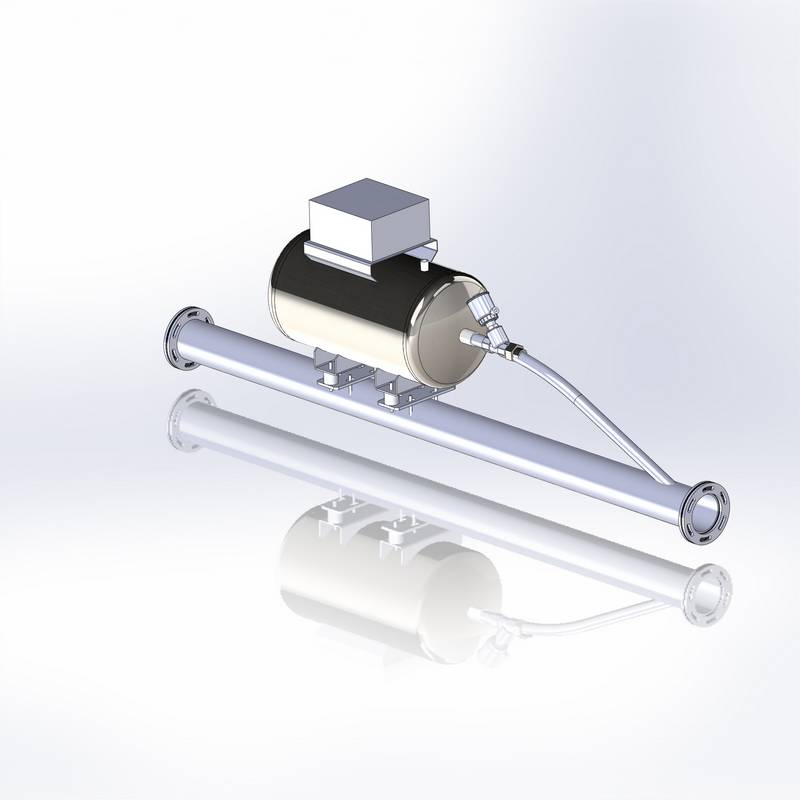
INTERMEDIATE TRIGGER
Intermediate triggers facilitate transfers over very long distances. By installing these triggers every 50 metres, we can ensure efficient, controlled transfers over distances of 500 metres and more. Thanks to our empirical knowledge of the positive pressure transfer process, we can easily manage their layout integration according to the product to be transferred.
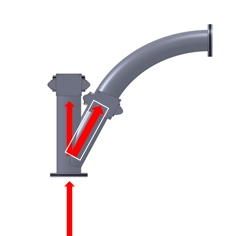
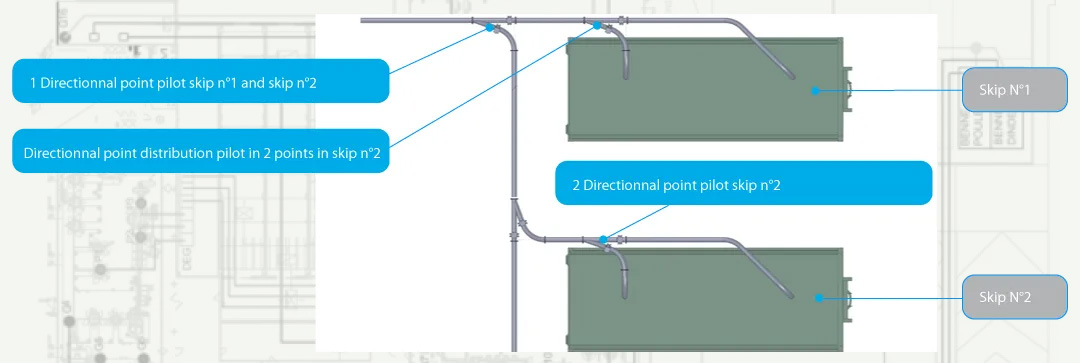
PIPE SWITCHES: DIRECTIONAL AND DISTRIBUTION
A switch allows directing the flow of the product in different directions. It functions like an intersection, allowing a choice between several paths. Switches are used to modify the route of your products, to split it into several branches, or to redirect it.
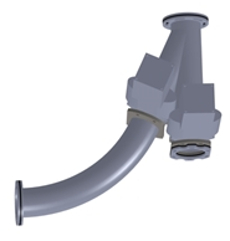
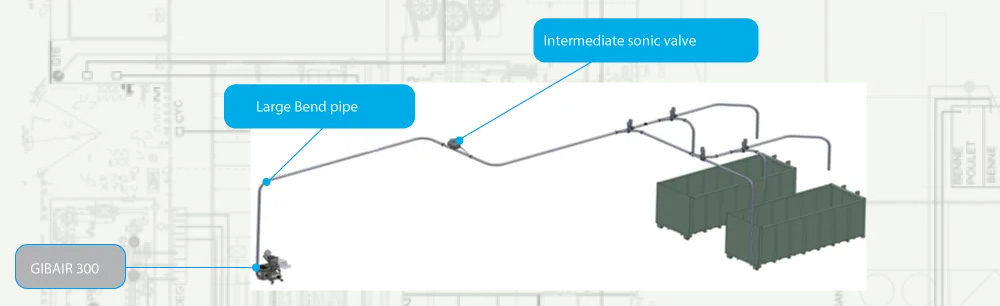
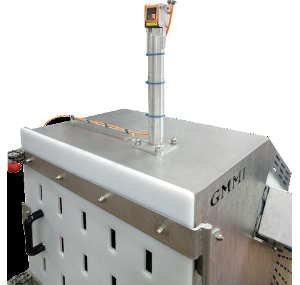
DETECTOR, RADAR SENSOR FOR VOLUMETRIC MEASUREMENT
The fill level sensor measures the fill level and offers total autonomy, for 100% autonomous operation of the transfer system. Depending on the product used, different models are available, ranging from laser sensors to laser wave or infrared sensors.
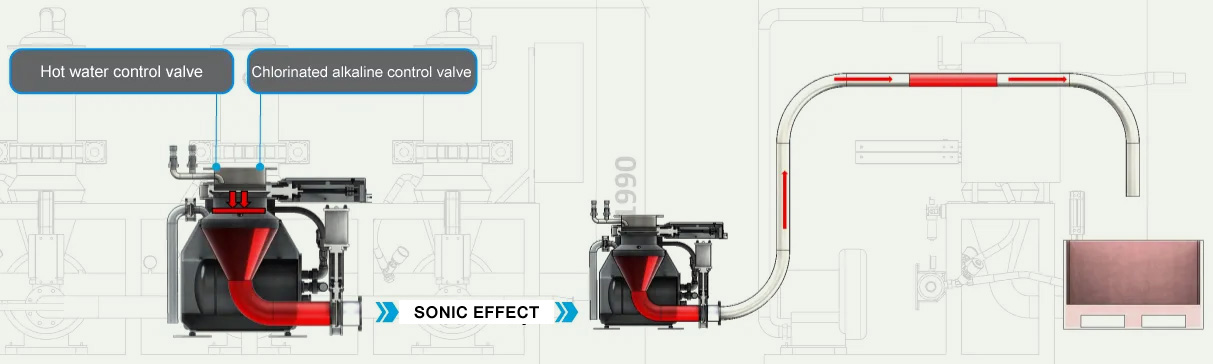
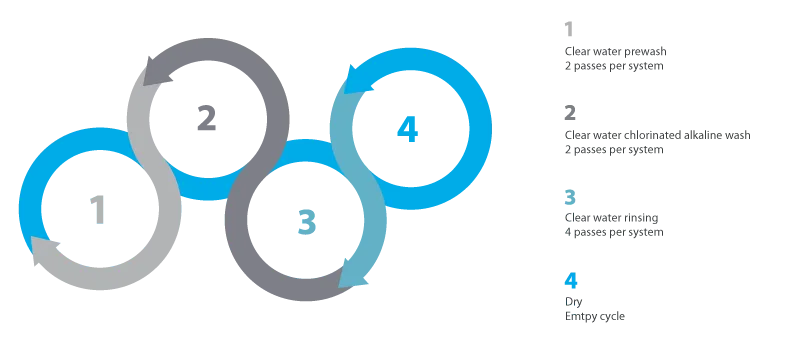
CIP, LAUNDRY IN LOST WATER
Laundry in lost water (programming by GIBAIR PLC): Hot water + Chlorinated alkaline.
“The sonic effect“ also allows the cleaning water to be conveyed at high speed through the network and thus achieve a efficient mechanical and chemical cleaning.
OUR CUSTOMER REFERENCES